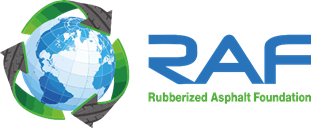
|
|
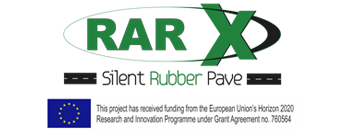
|
|
FIRST DEMONSTRATION PROJECT IN USA
|
|
Within the stated goal of the Board
of County Road Commissioners of the County of Kalamazoo is using their
expertise, energy and funds to provide the safest and most convenient road
system possible, and to contribute to economic development and high quality
of life throughout the county, it is not a surprise that when Michigan
Technological University (MTU) had an idea of who to contact with an idea,
the Road Commission of Kalamazoo County (RCKC) came to mind. Together it was decided to investigate
the usage of new technologies to enhance the future cost benefits of
preserving our infrastructure and provide future advancement of using scrap
tires in Michigan. A joint grant
application to the Michigan Department of Environmental Quality (DEQ) Scrap
Tire Development Grant was funded.
|
|
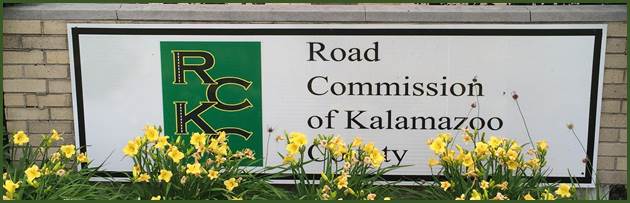
|
|
The first RARX (www.rarx.net) test sections, placed
under the leadership of the RCKC in Michigan, USA, were, in my opinion, was
one of best organized events of this kind, I have ever been a part of.
Weekly calls organized by Joanna I. Johnson, the Managing Director, prior
to the test section itself, the coordination at the job site and the yard,
the great “can do” spirit of all the personnel of the RCKC, MTU, asphalt
contractor and bitumen suppliers created an environment of positive
thinking, productivity and innovation that are, for me, the best I have
ever had the pleasure of participating. RCKC’s leadership made sure
everyone knew exactly what was going to happen and what was expected from
each participant. Simply FANTASTIC! As we know if any construction project,
the preparation is important and the flexibility of adapting to changes in
the field is also critical to delivering successful projects.
|
|
The purpose of the two RARX test sections were to investigate the
applicability of the usage of the new reacted and activated rubber (mainly
composed of finely grinded used car and truck tires) to create more cost
effective, long lasting, safe and environmentally friendly mixes and
surface treatments.
The test sections were supported by the grant from a proposal
elaborated by RCKC and Professor Zhanping You from MTU. CONSULPAV Lda
(www.consulpav.com)
cooperated with MTU in the formulation of a new kind of paving mix
incorporating large amounts of recycled rubber and recycled paving material
yet reaching rutting resistances and flexural fatigue lives with
performances much higher than most mixes used in USA. This mix was
denominated RARX-THINGAP. It contains about 6% RAP (reclaimed asphalt
pavement), regular PG 58-28 bitumen, about 4.5 % RARX and the rest is
selected natural aggregate (% by weight of the mix). RARX was provided by
CIRTEC (www.cirtec.es). Efforts by CONSULPAV
were covered by the SILENT RUBBER PAVE project
(http://silentrubberpave.eu/).
The asphalt contractor, Lakeland Asphalt, (http://lakelandasphalt.com/)
was very cooperative, enthusiastic, and inventive in adapting the mixing
process to incorporate the RARX material never used in the USA.
|
|
|
|
Placing RARX in
the conveyor belt at Lakeland Asphalt's plant
|
|
Even the bitumen supplier Bit Mat Products (http://www.bitmatproductsofindiana.com)
went out of its way to provide bitumen at higher than normal temperature,
so that we could minimize the heating time at the chip seal test section where
RARX was directly blending into the bitumen of the Bearcat RARX Distributor
(http://www.bearcatmfg.com/).
Bearcat designed a new kind of distributor to accommodate the capabilities
of this new pre-reacted and activated rubber with an extra auger inside the
tank to insure fast mixing of the RARX in the bitumen. Virtually
immediately after blending the asphalt rubber binder is ready to spray.
RCKC innovative spirit shinned as they provided an easy way to introduce
the RARX into the distributor tank.
This was also a first in the USA. The coordination provided by
Travis Bartholomew, Operations Director and Mark Worden, Project
Superintendent and the cooperative, professional, friendly attitude of all
the RCKC personnel made possible to the success of this project. Professor
You and students
participated in a very active role and were also vital for the success of
the project.
|
|
|
Loading system
developed by RCKC to place RARX into the distributor
|
|
The cost effectiveness of paving is clearly in the mind of the
paving industry in Michigan. See below a truck with 50 tons of RARX THINGAP
mix unloading into the paver.
|
|
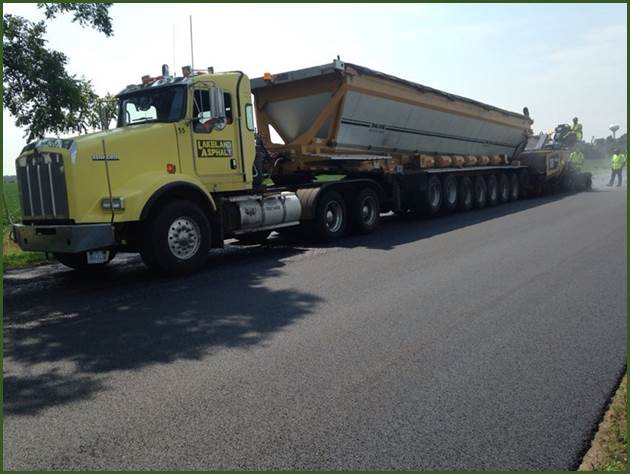
|
|
Below we can appreciate the general aspect of the section of the
road, a surface texture close-up and the stone on stone structure of the
RARX-THINGAP mix.
|
|
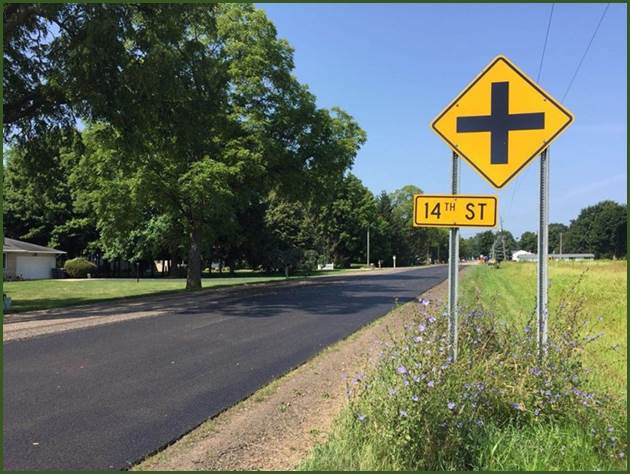
|
|
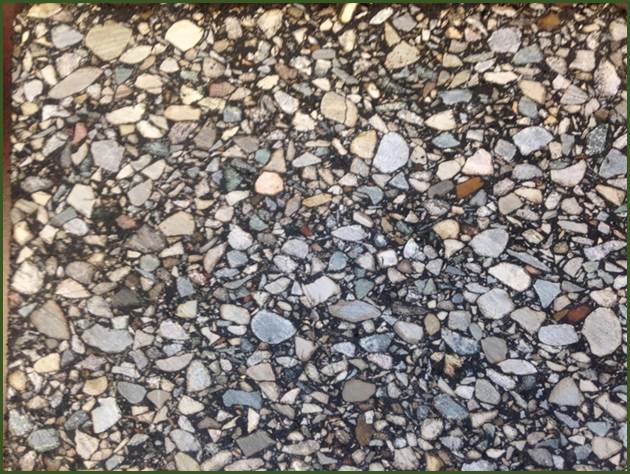
|
|
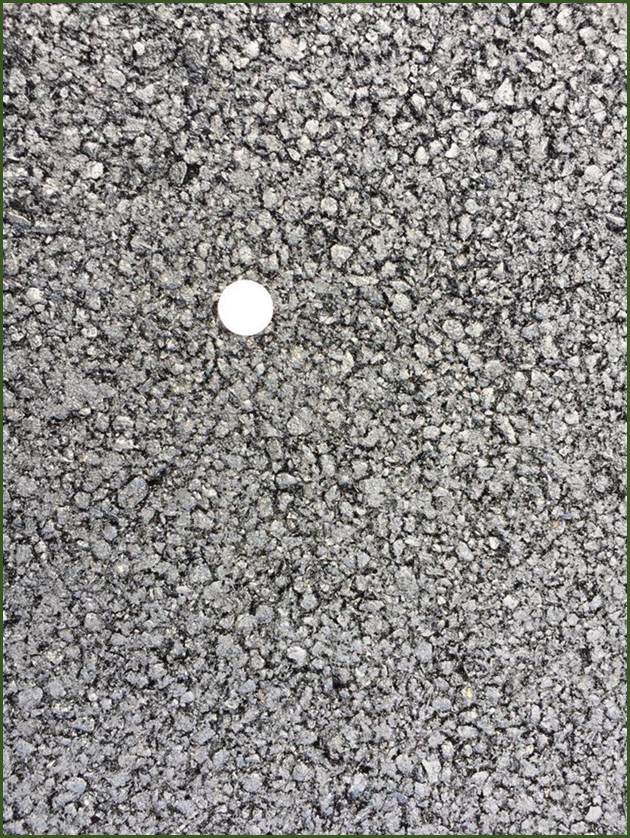
|
|
The RCKC team is very experienced in using chip seals in their
annual preventive maintenance strategies and they have had great success
using them. The purpose of the test section was to see if they can even be
more successful in making more long-lasting surface treatment. The video below shows the chip seal
application operation. I call your attention for the rollers that were
specially designed by RCKC. Again,
it shows RCKC desire for cost effectiveness as wider paving rollers
minimize the number of roller operators and number of passes allowing
faster operation. The chip seal trial was difficult and posed
challenges to properly apply the material in the beginning of the project.
The good story was that it eventually went well with quite some team effort.
There are certainly something we can do to
improve the equipment and training prior construction as well as other
opportunities to refine this process in the future.
|
|
|
Chip seal paving
|
|
The weather in Michigan is challenging, and requires that water be
prevented from entering into the pavement to minimize freeze thaw damage. Furthermore the snow removal equipment is very demanding
on the surface of those surface treatments. Only after the first winter we
will see how the new RARX rubber chip seal resist those harsh conditions.
For now they look good and they are expected to
out-last existing chip seal maintenance procedures.
|
|
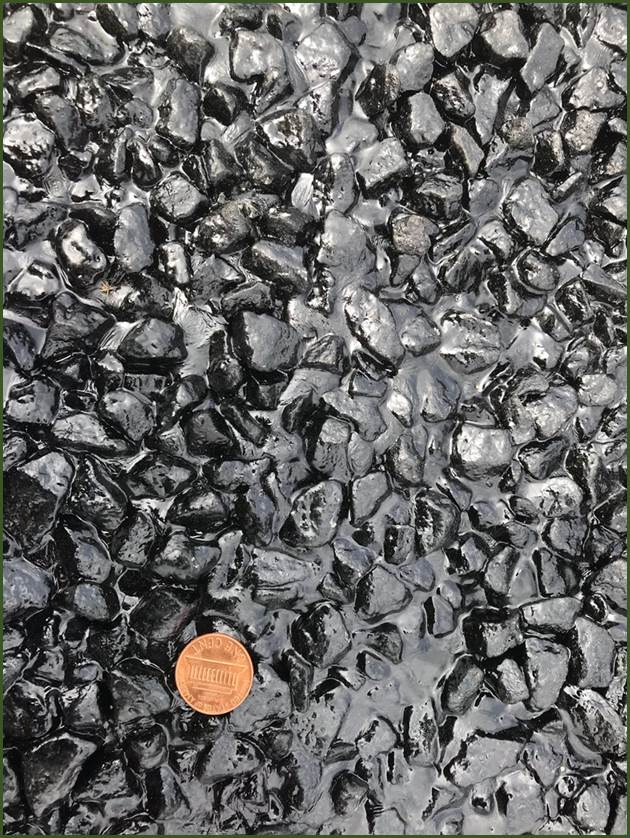
|
|
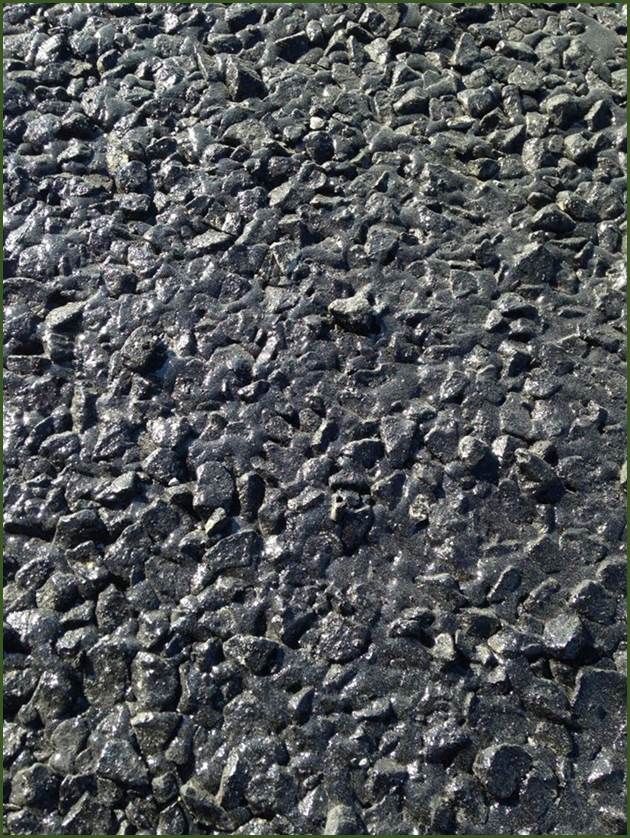
|
|
Furthermore, I am convinced that RCKC and the industry may be able
to advance and adapt the aggregate gradation selection to accommodate this
new rubberized binder and make it fit into their special requirements. With
the higher viscosity and with the much higher binder elasticity they are
able to place more binder, that if the market will support, may be less
expensive, and secure more aggregate retention and resistance to
reflective cracking while being also less prone to aging.
It was very exciting and gratifying participating in this very
important first RARX demonstration project in the USA. As the
Rubberized Asphalt Foundation (RAF) is a research foundation dedicated to
the science and practical use of recycled tire rubber in asphalt. RAF
serves as a comprehensive, expert resource to provide technical knowledge
and awareness that will enhance the development and broad use of rubberized
asphalt. The foundation is comprised of renowned international experts from
academia, government and industry who are leading the scientific
development of recycled rubber for asphalt applications. This project confirmed that recycled materials
can potentially create a sustainable circular economy where RARX recycled
rubber can be used for asphalt applications. A potential mix of fixes in
future sustainability of our infrastructure. The RARX THINGAP mix placed by RCKC is
likely to be one of the quietest mixes most cost effective, environmentally
friendly and safe mixes ever placed in USA.
As Joanna Johnson stated “we
are pleased to be part of a first use of this product; learning during the
preparation and application process.
Now we will monitor and potentially this could be the beginning of
something new “.
|
|
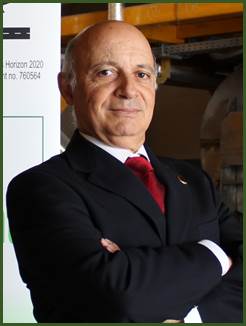
|
|
Dr.
Jorge B. Sousa
Director
Rubberized Asphalt Foundation
|
|
|
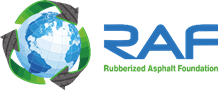
|
|
|
|